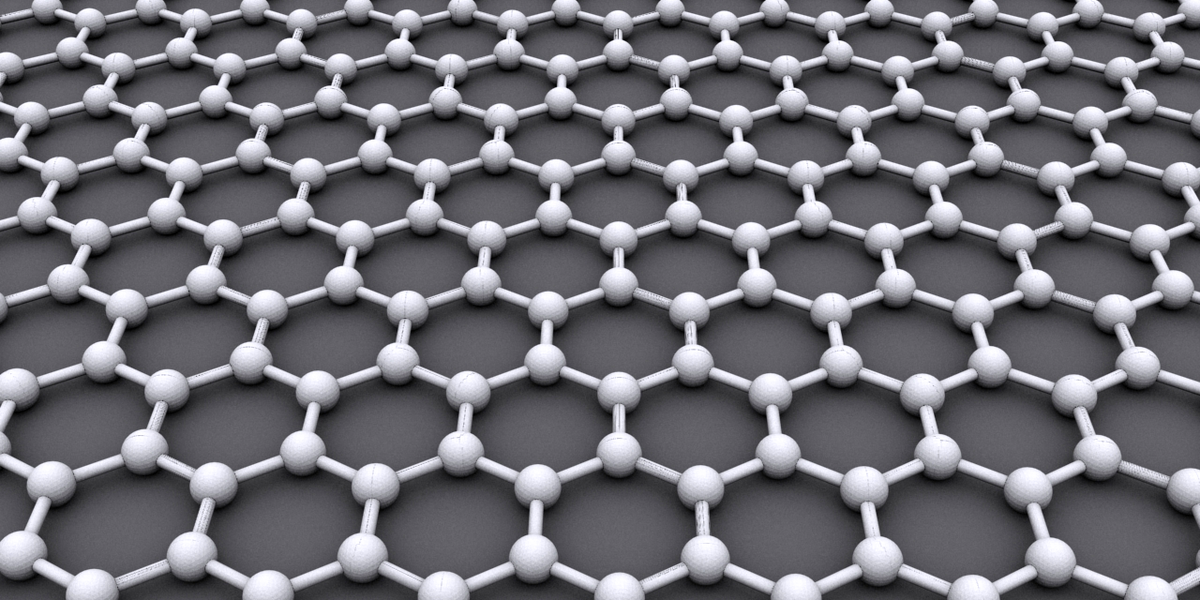
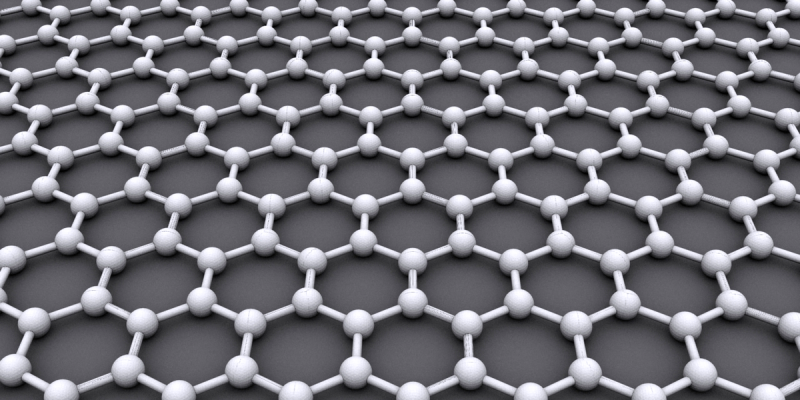
The use of aluminium in wiring is unlikely to bring a smile to the face of anyone who has had to deal with it in a 1960s, or early 1970s-era house. The causes behind the fires and other accidents were myriad, including failure to deal with the higher thermal expansion of aluminium, the electrically insulating nature of aluminium oxide, and the general brittleness of aluminium when twisted.
Yet while copper is superior to aluminium in terms of electrical conductivity and ease of installation, copper prices have skyrocketed since the 1970s, and are on the verge of taking off to the moon. A big part of the reason is the increased use of copper in everything from electronics and electrical motors to generators, driven by large-scale deployment of wind turbines and electrical vehicles.
As the world moves to massively expand the use of electrical cars and installation of wind turbines, copper demand is predicted to outstrip current copper supply. With aluminium likely to make a big return as a result, it's worth taking a look at modern-day aluminium-based wiring, including copper-clad aluminium and the use of carbon-based replacements.
How to Make Copper Expensive
In hindsight, copper prices weren't that bad yet in the 1960s and 1970s, as we can see in the following graph of copper prices of the past 45 years:
Copper prices per pound - 45 year historical chart. (Source: Macrotrends.net)
These price increases are driven largely by an increasing demand for more electrical vehicles and wind turbines, which over the coming years look to accelerate, putting further pressure on the existing supplies. Although the USGS has identified likely undiscovered copper resources, this does require for a mining operation to be established, and not all copper ore can be economically mined and turned into raw copper.
Earlier this year the International Energy Agency (IEA) released a report on the role of critical minerals in the energy transition to low-carbon sources. Taken from this report, in the below images we can see the relative metal requirements per type of source, per rated output capacity, as well as the material requirements for electrical vehicles (EVs) compared to conventional (ICE) cars:
Minerals used in clean energy technologies compared to other power generation sources (Source: IEA)
Minerals used in electric cars compared to conventional cars. (Source: IEA)
Meanwhile, the expected demand curve for copper in light of current sustainable development policies at the same time is expected to look something like the below image, contrasted against current copper mines output and expected new mining operations.
Committed mine production and primary demand for copper, 2020-2030. (Source: IEA)
Not unsurprisingly, since many of such policies have come into effect around 2000 and alongside increasing demand from other industries, copper prices have been steadily rising, far beyond the highs of the 1960s that made prospective home owners decide between installing copper or aluminium wiring.
At this rate, we might see the end of common use and easy availability of copper in a matter of years. At the same time, as copper's properties make it ideal for certain applications, other uses that may be fine with alternatives may have to look elsewhere. Very likely this would mean that everything from house wiring to customer electronics may soon find itself priced out of the copper market. What alternatives are there, and how do they compare to copper?
Trying to Top the Best
Copper is a favorite for electrical wiring for a number of reasons, not the least of which are its excellent thermal and electrical conductivity. This is why copper is a preferred material for heatsinks, and for electrical wiring in both houses and in electrical devices. In comparison, pure aluminium has only 61% of the electrical conductivity of copper by cross-section.
Yet aluminium has one major benefit over copper, and that is that it is twice as electrically conductive by mass, owing to copper's density at room temperature of 8.96 g/cm3, versus 2.70 g/cm3 for aluminium. For this reason applications where weight is more of a concern such as transmission and distribution wiring. Especially when running large bundles of cables between pylons, the higher conductance to weight ratio of aluminium offers major benefits.
Cross section of copper-coated aluminium (CCA) wire. (Source: Fujikura Ltd.)
When properly installed and used, aluminium is a fine choice as electrical conductor, but that doesn't mean that it is the only option. Something that's commonly seen in wiring since the 1970s is copper-clad aluminium (CCA) wire. This is basically what the name says: an aluminium core that is clad in copper, making it a bimetal. The main goal of CCA is to combine the benefits of both copper and aluminium in a single wire, meaning closer to copper-like conductivity, while avoiding the pitfalls of aluminium as the installation method is the same as for copper wire.
If we take a look at the specifications which Fujikura lists for CCA (also called CAW), we can see that while CCA isn't as good as solid copper wire, it is significantly better than solid aluminium wire. If we add to this the major benefits that a copper skin adds in terms of near-elimination of thermal creep and compatibility with copper-compatible termination methods and technologies, it would seem to form a good alternative to both.
Interestingly, CCA has been competing with both copper and aluminium wiring for a while now, particularly for building wire, as noted in this excellent write-up by the IAEI Magazine on the history of aluminium building wiring. An important detail that this article adds is that the creation of CCA is fairly labor-intensive, meaning that its popularity has always been dependent on the current copper prices.
The IAEI notes that until late 2005, copper prices were still fairly low (as noted in the earlier historical copper prices graph) , but have since risen to the point where CCA is now highly competitive with copper.
A Dash of Carbon
The various allotropes of carbon.
CCA is not the pinnacle of materials science when it comes to electrical conductors. Carbon-based structures, such as carbon nanotubes (CNTs) have much higher electrical conductivity than copper, as does graphene. The main issue is that making wires out of them is not exactly straightforward. Yet what if they could be merged with a metal like aluminium, or even spun into wires?
An article by Lekawa-Raus et al. published in 2014 titled Electrical Properties of Carbon Nanotube Based Fibers and Their Future Use in Electrical Wiring examines the research literature at that point in time on the production of CNT fibers, which can be spun into CNT wires. Based on the research, these wires would have superior electrical conductivity and weight, outperforming both copper and aluminium handily on all counts.
Connecting these CNT wires could be handled with a carbon solder, which at the time was under development at Cambridge. Even so, many challenges in producing flawless CNTs with the appropriate morphology remained, especially when moved from a laboratory to an industrial setting. Many of these concerns remain in 2020, when Cesano et al. performed another review study. They note that although progress has been made in the intervening years, full-carbon wires are still a future prospect.
Even so, CNT fibers can be commercially purchased for not entirely insane amounts of money, as well as CNT composites with copper and other metals like silver and gold. Recent studies by Zhang et al. (2018), Pradhan et al. (2020) and Chyada et al. (2017) show improvements in thermal conductivity and electrical conductivity as well as tensile strength respectively for graphene-aluminium composites.
The addition of CNTs has also found use in other applications, such as the mechanical reinforcement of aluminium parts, with Nyanor et al. (2020), detailing an aluminium matrix reinforced with CNTs as well as micron-sized titanium-carbide (TiC) particles. This creates a material that has 2.3 times the hardness of pure aluminium, with significantly improved wear resistance.
The Yazaki company of Japan has filed numerous patents on Al-CNT composite materials that are intended to be used in upcoming wire products. Tirupati Graphite Plc meanwhile has made claims about an Al-graphene composite that claims to have copper-like electrical conductivity, better thermal conductivity than copper and better micro-hardness than copper.
Electrifying Changes
With sky-high copper prices a potential prospect over the coming years, it would seem pertinent to take a good hard look at the available alternatives. Whether CCA is an acceptable alternative to copper depends on a lot of factors, but with real-world usage data available for the past five decades for house wiring and other applications, it is at least a known quantity.
Perhaps more exciting is the prospect of graphene and CNT-based wiring, which offers more than just a trade-off compared to copper. Instead these may result in an alternative to copper that is actually better in all respects, with better conductivity, higher tensile strength, higher resistance to corrosion and higher conductivity for both a given cross-section and weight.
From a hobbyist perspective, CCA is probably the most likely alternative one will end up with, based on a cost perspective and ease of handling. As it behaves and can be processed similarly to copper wire including soldering using standard solder alloys, it can replace copper wire with just a small bump in diameter to compensate for the worse electrical conductance.
It would be rather cool if future generations are wiring up their projects with CNT wires and carbon-based solders, however. Here's to more carbon in our future.
#currentevents #featured #science #carbonnanotubes #cca #cntwire #copper #coppercoatedaluminium