#cement

https://www.dailymotion.com/video/x91tfai )
Researchers have made a #supercapacitor out of #cement and #carbon black, which is similar to #charcoal.
A supercapacitor is an alternative to a #battery, capable of #storing #energy and releasing it very quickly.
If this new tech is scalable, it could be huge in the effort to shift toward renewable energy.
There’s a well-known problem with renewable energy—it’s not constantly available. The sun can go behind a cloud and deprive solar panels of their power source, or the wind can not blow and render wind turbines completely useless. If we’re ever going to be able to transition entirely to green energy, we need to find a solution that allows us a constant stream of power.
In other words, we need to be able to store energy as we collect it. As a result, there is a whole lot of interest in the development of things like batteries and capacitors, both of which store energy. Make the perfect energy storage container, and you revolutionize the entire energy industry.
Recently, a group of researchers from MIT and Harvard released a new study announcing that they have discovered a new and exciting way to do just that. Well, “new” is an interesting word here. While the combination and the use case is definitely new, the ingredients are old— really old.
The solution to our green energy storage problems could just be cement and carbon black.
“The material is fascinating, because you have the most-used manmade material in the world, cement, that is combined with carbon black, that is a well-known historical material — the Dead Sea Scrolls were written with it,” Admir Masic, one of the authors of the study, said in a press release. “You have these at least two-millennia-old materials that when you combine them in a specific manner you come up with a conductive nanocomposite, and that’s when things get really interesting.”
Related video: Nuclear Fusion Reactor For Cleaner Energy (Dailymotion)
Now, one of those things you’ve almost definitely heard of—the title of “most-used manmade material in the world” is not awarded lightly. And carbon black is basically just very fine charcoal that comes from an incomplete combustion process. So this material is nothing crazy high-tech when you break it down into its constituent parts.
But Masic wasn’t lying when he said that “things get really interesting” when you combine them. Mixed together, cement and carbon black create what is called a supercapacitor—an alternative to a battery that can store a very large amount of electrical energy and release it very quickly on demand.
Carbon black is hydrophobic, meaning it doesn’t mix with water. So, when added to wet cement, it clumps up into strands and voids between pockets of the goopy substance. In doing so, the carbon black—which is also highly conductive—basically forms its own network of wires as the cement hardens. Once that occurs, the entire substance is dunked in an electrolyte like potassium chloride long enough for the material to absorb charged particles.
If you make two electrodes out of this material and separate them with a thin insulator, you have your brand-new rechargeable supercapacitor.
But superconductors have been made before. That’s nothing new. What’s most exciting about this discovery is that it’s basically lightly-altered cement—an incredibly common building material. Because you don’t actually need to add very much carbon black to standard cement to create this supercapacitor, the cement is still strong enough to be used in buildings. You could build the foundation of a house out of this material and be able to store enough energy to power that house for an entire day.
And researchers don’t want to stop there. Another potential application they’re particularly excited about is building roadways. If you basically build a road out of a battery, it could be used to charge electric cars as they pass over top, giving them a little boost to just keep on driving. Different applications would likely need different variants of the material, but it’s all based on the same new tech.
Right now, researchers are excited by the potential and apparent flexibility of that new tech. The next challenge is scaling up, as the team is currently working with a small sample. But if they can get this to work on a practical and useful scale, the sky may be the limit for green energy."


Cement recycling method could help solve one of the world’s biggest climate challenges
Researchers from the University of Cambridge have developed a method to produce very low-emission concrete at scale – an innovation that could be transformative in the transition to net zero.
But it's energy intensive...

"Furno bets that super-efficient, modular kilns will turn the cement industry upside down."
"Calcium containing minerals, usually from limestone, are sent through the kiln, where they're heated to more than 1,110 degrees F (600 degrees C)."
"Raw materials enter one end of the kiln, which lies horizontally, and are pushed past an intense flame to the other end, where they emerge as clinker."
"Kilns today are not very efficient. A study of one in China showed that only about 30% of the heat in the kiln powered the calcination reaction; the rest was lost."
"Furno's kiln, on the other hand, is far more efficient, reducing emissions from fossil fuels by 70% or more. It accomplishes that by turning the kiln vertical, filling it with ingredients that are ground to prescribed dimensions, and then seeping through it a combustive gas (natural gas, biogas or hydrogen) and setting it ablaze."


Ancient Roman cement/concrete is better in many ways than modern cement/concrete. So why don't we use it today? Like McArthur Park, we lost the recipe.
#AncientRome #AncientRoman #Rome #Roman #Concrete #Cement #buildingMaterials

https://www.bitchute.com/video/0JpcEmCbScKD/
#building a #newearth
‘ #Cellular #Cement’ w #AirCrete #Harry - The #BioCharisma #Podcast S2 Episode 18
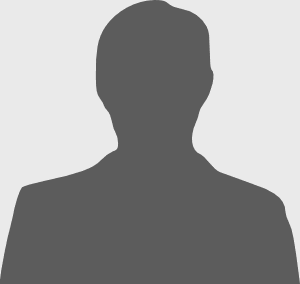
To #decarbonize #cement, the #industry needs a full transformation ...
#Cement #production has an enormous #carbon footprint. That can be curbed with plug-and-play #solutions, but eliminating #emissions entirely will require big, ambitious action...
https://grist.org/energy/to-decarbonize-cement-the-industry-needs-a-full-transformation/


straight to hell for these #evil #ones
https://www.bitchute.com/video/6AiEd4ZQuJCI/
#Israel pours #cement over #springs in the #city of #Hebron to prevent #Palestinians from using them


Odd day for it at just above freezing and a big #snow #storm in the offing, but our #railway line contractors were out today pouring #cement via an overhead #concrete #pump used at maximum reach to apparently create the bridge deck on our #railway #bridge. If it ever gets finished this will be part of our light rail system here in #Ottawa. It is already a full year behind schedule.


Cement and concrete industry publishes roadmap to reach net-zero emissions by 2050
Forty leading international cement and concrete manufacturers have published a plan to eliminate carbon emissions from one of the world's most polluting industries.
The commitment has been made by members of the Global Cement and Concrete Association (GCCA). Together, they represent nearly 80 per cent of the industry outside China.
Published ahead of next month's COP26 climate conference, the roadmap includes an intermediate pledge to reduce greenhouse gas emissions by up to 25 per cent by 2030. This could prevent an estimated five billion tonnes of CO2 emissions.
"We now need swift and decisive political action"
"We highly welcome the industry’s ambitious climate protection targets set forth in the GCCA’s 2050 roadmap," said HeidelbergCement CEO Dominik von Achten."Together, we are doing everything we can to achieve them."
Earlier this year, HeidelbergCement announced plans to eliminate carbon emissions from a plant in Sweden by upgrading the factory with technology that captures carbon emissions.
"We now need swift and decisive political action to create the right framework conditions, particularly in the area of CO2 infrastructure and market incentives for low-emission building materials," von Achten added.
UK Concrete director Chris Leese also called for government support.
"It’s now critical as we head towards COP26 that the UK industry sees a package of policy measures that will support decarbonisation over the coming decades," he said.
The roadmap is aligned with the Paris Agreement to limit global warming to 1.5 degrees Celsius and follows a similar roadmap published by the UK cement industry showing how it could achieve net-zero by 2050.
The cement industry is responsible for seven per cent of the world's CO2 emissions. The roadmap sets out seven steps to achieve net-zero emissions by 2050.
Roadmap includes reducing fossil fuel and clinker use
Substituting high-carbon clinker, which is the main ingredient in Portland cement, with lower-carbon materials will contribute to lowering the CO2 footprint of both cement and concrete, according to the roadmap.
A commitment to significantly reducing fossil fuel use in manufacturing and increasing the use of alternative fuels will also contribute to lowering the CO2 footprint.
The industry has committed to building 10 industrial-scale carbon capture plants by 2030, building on current pilots in North America, India, China and Europe.
New chemical substitutes for clinker and concrete mix play an important role in the roadmap, with the plan to build on approaches that are already in the research or development phase.
Investments in kiln technologies and more research will also be implemented. The GCCA will utilise its global research network, Innovandi, to advance the research.
Additionally, a global innovation challenge that matches startups with GCCA member companies will take place.
The GCCA will create a procurement framework that the industry can use during construction to improve efficiency in the design and use of concrete during construction.
This will involve using recycled materials, extending the lifetime of projects and more efficient use of resources.
Support from governments and policymakers needed
The roadmap requires policymakers, governments and multilateral organisations to play their part in supporting a circular economy and the development of new technologies.
GCCA members have committed to reaching this target without using offsets, and the organisation claims it can achieve net-zero emissions even if the global cement and concrete products market doubles as expected from $333 billion in 2020 to $645 billion in 2030.
Net-zero means that an entity such as a company, industry sector or country makes zero contribution to atmospheric CO2 across its entire value chain.
Cement is a huge source of carbon emissions, largely because it relies on clinker made from crushed and burned limestone. This process separates the calcium, which is a key ingredient in cement, from the carbon, which is released into the atmosphere. Emissions are also generated by heating the kilns to above 1,000 degrees Celsius to process the limestone.
Companies in the architecture and design sector that have committed to becoming net-zero include Swedish cosmetics brand Forgo and British car manufacturer Rolls Royce.
Dezeen has also pledged to become a net-zero business by 2025.
The post Cement and concrete industry publishes roadmap to reach net-zero emissions by 2050 appeared first on Dezeen.

#Cement makers across world pledge large cut in #emissions by #2030 | #ConstructionIndustry | The Guardian
This could be quite significant.

Carbon-capturing Celour paint allows anyone to "participate in CO2 removal in their daily lives"
Design graduate Kukbong Kim has developed a paint made from demolished concrete that is capable of absorbing 20 per cent of its weight in carbon.
Called Celour, the paint can sequester 27 grams of CO2 for every 135 grams of paint used.
"That is the same amount of carbon dioxide that a normal tree absorbs per day," Kim said.
The indoor-outdoor paint is made of waste concrete powder, a cement-based residue from concrete recycling that is normally buried in landfills, where it can alkalise the soil and have a detrimental effect on local ecosystems.
Celour is a carbon-capturing paint that comes in three colours
Through a chemical process called mineral carbonation, which takes place when the paint reacts with the CO2 in the surrounding air, Kim says Celour can reabsorb a significant part of the emissions that were generated by producing the cement in the first place.
Eventually, she hopes to optimise the capturing capacity of the paint so that it completely negates the carbon footprint of the cement it is made from.
"I think it is too early to describe Celour as carbon neutral," Kim said. "It needs further study but I want to make it a carbon-negative product. That is my goal."
"It's not enough if we just stop emissions, as we already have high levels of CO2 in the air," she added. "We need to participate in CO2 removal in our daily lives."
Concrete naturally reabsorbs some of the carbon it emits
Cement is the most carbon-intensive ingredient in concrete and is responsible for eight per cent of global emissions.
But when concrete is recycled, only the aggregate is reused while the cement binder is pulverised to create waste concrete powder and sent to landfill, where it can disturb the pH balance of the surrounding soil.
"Waste concrete powder is high in calcium oxide," Kim explained. "And when it is buried and comes into contact with groundwater or water in the soil, it turns into calcium hydroxide, which is strongly alkaline."
The waste concrete powder is filtered, pulverised and mixed with a binder, water and pigments
With her graduate project from the Royal College of Art and Imperial College London, the designer hopes to show the usefulness of this industrial waste material by maximising its natural ability to capture carbon.
Studies have shown that cement already reabsorbs around 43 per cent of the CO2 that is generated in its production through the mineral carbonation process.
This is set off when concrete is cured by adding water, which reacts with the calcium oxide in the cement and the CO2 in the air to form a stable mineral called calcium carbonate or limestone.
A traditional concrete block continues to cure throughout its life but because this process is reliant on exposure to air, only its outer layers will react with the CO2 while its core will remain uncarbonated.
Celour could store carbon for thousands of years
But Kim was able to improve the material's carbon-capturing capabilities by turning the waste concrete pounder into a paint, mixed with a binder, water and pigments.
This is spread thinly on a surface so that more of the material is exposed to the air and can carbonate.
In addition, the coarse powder was further filtered and pulverised to increase the relative surface area of the particles while a polyvinyl alcohol (PVA) binder creates small gaps for air to enter.
"I have done a lot of experiments with different ingredients to maximise carbon absorption by increasing the surface area that comes into contact with carbon dioxide in the air," she explained.
"Graphene, which can capture lots of carbon thanks to its structure, was also considered as a binder but excluded because it is currently priced high and cannot be mass-produced."
The paint can be used both indoors and outdoors
Cement has long been used to create traditional paint, which is also capable of sequestering CO2. But Kim hopes to harness these carbon-capturing benefits while keeping a polluting waste material out of landfills and avoiding the emissions associated with making new cement.
How long the paint is capable of storing carbon is dependent on what happens to it after it is no longer needed. But Kim says it could be locked away for thousands of years unless exposed to extreme heat, which would alter the chemical structure of the carbonate.
As part of our carbon revolution series, Dezeen has profiled a number of carbon capture and utilisation companies that are working on turning captured CO2 into useful products from bioplastic cladding to protein powder and concrete masonry units.
The post Carbon-capturing Celour paint allows anyone to "participate in CO2 removal in their daily lives" appeared first on Dezeen.
#all #products #design #royalcollegeofart #productdesign #concrete #studentprojects #materials #graduates #paint #cement #carboncapture #carboncaptureandutilisation #mineralcarbonation

Sweden faces "very serious" economic impacts as environmental ruling closes cement plant
The closure of Sweden's biggest cement factory on environmental grounds could cause up to 400,000 job losses and wipe out the country's GDP growth, according to an alliance of construction bodies.
Work could grind to a halt on three-quarters of all house-building projects and the construction sector could lose more than 20 billion Swedish Kronor (SEK) per month.
Work on infrastructure projects including Foster + Partners' Slussen masterplan in Stockholm could also be impacted.
The warning came from Byggföretagen, a body that represents construction firms in Sweden.
"Sweden is facing an extensive construction halt," it said. "By November, three out of four new homes will not be able to start construction. Several major infrastructure projects are stopped or delayed. Between 200,000 and 400,000 jobs are threatened."
Cement plant license rejected on environmental grounds
Byggföretagen based its figures on an impact assessment prepared in the wake of a decision by Sweden's Supreme Land and Environmental Court last week to reject a new licence for the Cementa cement plant at Slite in Gotland.
"The construction industry's share of GDP is about 11 per cent," Byggföretagen said. "The industry contributes almost SEK 40 billion in tax revenue to health care, schools and care. The construction halt thus risks displacing the entire GDP growth in 2022."
Top image: the limestone quarry on Gotland. Above: the Cementa plant is set to close
The plant, which is the second-largest source of greenhouse gas emissions in the country and responsible for three per cent of all Sweden's CO2 emissions, will no longer be able to mine limestone as a result of the ruling.
The licence was refused due to concerns over the plant's environmental impact assessment, particularly in relation to the impact on groundwater. Greenpeace has also accused the plant of using its kilns to incinerate toxic waste without a permit.
The court was concerned about high levels of chloride pollution in groundwater samples taken near the site, according to Swedish news organisation Dagens PS.
"The fact that environmental problems at one cement factory can send the whole construction industry of a country into a panic puts a light on both the climate crisis and critical supply chain and infrastructure problems in Sweden," Dagens PS journalist Daniel Jacobs told Dezeen.
Slite plant to be converted into carbon-neutral factory
The ruling means that the plant, which produces three-quarters of all the cement used in Sweden, will have to cease production on 31 October. Byggföretagen has demanded an urgent meeting with the government to discuss the ruling.
"The situation is very serious," said Byggföretagen's CEO Catharina Elmsäter-Svärd. "Sweden is facing an extensive construction halt. The cement shortage will have extensive consequences for the Swedish economy and employment."
Cement production is responsible for an estimated eight per cent of global carbon emissions. The Slite plant has been earmarked for conversion into an experimental carbon-neutral factory by 2030 but parent company HeidelbergCement told Dezeen the court ruling could impact the timetable of the project.
Carbon revolution
This article is part of Dezeen'scarbon revolution series, which explores how this miracle material could be removed from the atmosphere and put to use on earth. Read all the content at: www.dezeen.com/carbon.
The sky photograph used in the carbon revolution graphic is byTaylor van Riper via Unsplash.
The post Sweden faces "very serious" economic impacts as environmental ruling closes cement plant appeared first on Dezeen.